In the current fast-paced manufacturing landscape, the need for speed and efficiency has never been more critical. As competition increases and consumer requirements evolve rapidly, manufacturers meet the task of delivering high-quality products in lesser timeframes. This is where rapid injection molding comes into play, revolutionizing the way products are created and brought to market. By leveraging advanced technologies and optimized processes, manufacturers can significantly reduce delivery times while maintaining precision and quality.
Rapid injection molding is not just a trend; it is becoming an essential tactic for organizations looking to stay at the forefront. This cutting-edge approach allows for quicker prototyping and production, enabling manufacturers to evaluate their prototypes and execute adjustments swiftly. As a consequence, companies can react to market changes and customer responses with remarkable agility. Utilizing rapid injection molding can reveal new opportunities for productivity, ultimately resulting to enhanced profitability and customer satisfaction.
Benefits of Rapid Injection Molding
Accelerated injection molding provides manufacturers the ability to significantly cut down production lead times. Traditional molding processes can take several weeks or sometimes months to set up and produce initial parts, but with accelerated injection molding, manufacturers can streamline the development and prototyping phases. This speed enables companies to launch their products to market faster, which is essential in today's competitive landscape where timing can be a crucial factor for success.
Cost efficiency is another key advantage of rapid injection molding. By utilizing cutting-edge technologies and techniques, manufacturers can lower the costs associated with tooling and production. The ability to manufacture molds quickly and at a lower expense results in decreased production costs, making it feasible even for smaller production runs. This means that businesses can be more adaptable, trying out with new designs and variations without the threat of significant financial loss.
Furthermore, accelerated injection molding supports enhanced design flexibility. Manufacturers can easily modify existing molds or create new ones, which allows them to respond to changing market demands or customer preferences. This adaptability is crucial as it permits for quick iterations and improvements to products, guaranteeing that manufacturers stay in front of their competitors by offering creative solutions that meet consumer needs.
Fundamental Techniques Fueling Swift Molding
The development of computer-assisted design (CAD) tech substantially enhances the functions of quick molding. By utilizing sophisticated models and modeling, companies can see and optimize the layout of forms ahead of they are even manufactured. This quick prototyping facilitates fast iterations, which ensures that potential issues are recognized early in the development stage. Consequently, producers can create premium forms more efficiently, resulting in quicker item releases.
Another important aspect influencing fast inject is the adoption of innovative substances. New polymer formulations and composite materials provide manufacturers with more adaptability in picking the right properties for their goods. Such advanced materials not only enhance strength and endurance but also reduce cycle times and streamline the forming procedure. As manufacturers test with a wider variety of resources, they can develop customized approaches that meet precise market requirements rapidly and successfully.
Ultimately, automation and smart production technologies hold a pivotal function in optimizing rapid forming procedures. The combination of robotic systems and IoT solutions allows for real-time oversight and management of the forming system. Robotic systems can adjust parameters on the spot, ensuring maximum efficiency and reducing idle time. Such shift towards mechanization not just accelerates production and additionally boosts consistency and excellence, thus making quick molding a considerably dependable option for manufacturers seeking to keep competitive.
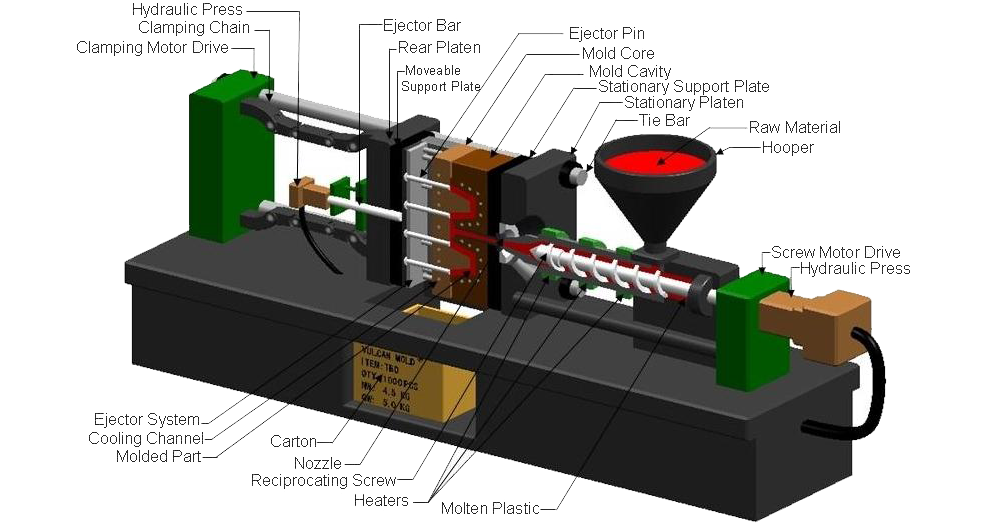
Practical Applications and Case Studies
Rapid injection molding has transformed multiple industries by allowing for quicker production cycles without sacrificing quality. One notable example is in the medical device sector, where companies have leveraged this technology to enhance the development of surgical tools and implants. By enabling quicker prototyping and testing of components, manufacturers can react more swiftly to regulatory requirements and market demands, ultimately leading to improved healthcare solutions.
In the automotive industry, quick injection molding has been crucial in the creation of prototype parts and end-use components. A leading car manufacturer implemented this approach to produce design models of new vehicles for market testing. This permitted them to gather consumer feedback early in the design process, significantly reducing the time to market for their newest models. The ability to make rapid iterations on designs has not only improved efficiency but also improved the final product’s conformance with consumer expectations.
The electronics market has also benefited from rapid injection molding, especially in manufacturing enclosures and components for devices. A technology company faced delays due to traditional molding methods that did not meet their fast-paced innovation cycle. By switching to rapid injection molding , they were able to reduce production lead times from months to weeks, enabling them to maintain a competitive edge in an ever-evolving landscape. This agility has proven vital for manufacturers aiming to keep pace with technological advancements.